- Top
- Our product
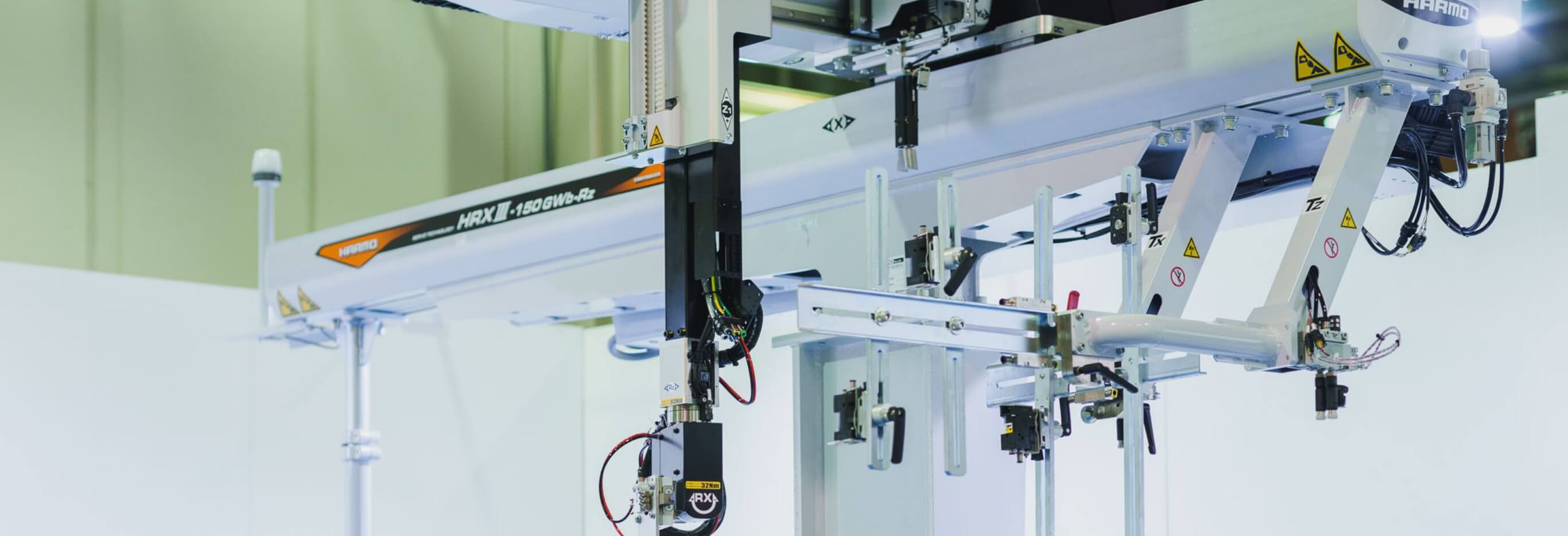
We offer a line of comfortable, safe, and highly productive injection molding products.
We are the only company in Japan who produces all the box robots and peripheral automation devices needed for injection molding of plastic products. We provide complete and optimal solutions to solve the wide range of issues that our customers face, such as automation/personnel saving on injection molding lines, as well as for productivity, measures against defective products, and stable quality.
- Dealing with insufficient personnel
- Automation at production sites
- Eliminating human error
- Shortened planning time
- Stable quality of molded products
- Detection of equipment abnormalities
- Reduced raw material costs
- Prevention of wasted materials
- Ascertainment of the causes of defective products
- Molded part takeout robots
- Gran cutters
- Dehumidifying dryers
- Hopper Dryer
- Hopper Loader
- Mold temperature controllers
- Stock system
- Automatic packaging machines
- Attachment for EOAT
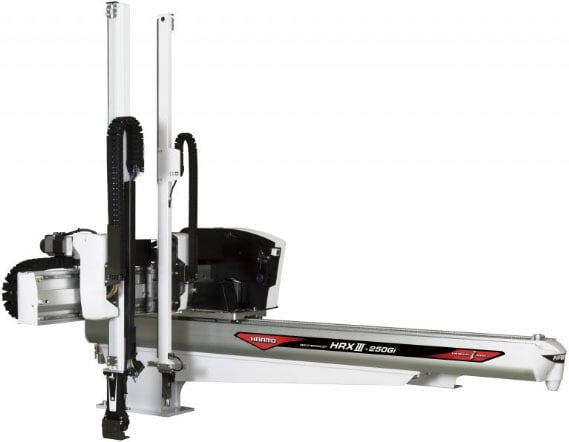
We have a broad line-up of products, for ultra-small molding machines with 15 tons of clamping pressure to ultra-large molding machines with 4,000 tons of clamping pressure. With our line-up of arm structures that suit the configuration of your injection molding machines and drive types of various characteristics, we can propose the most optimal robot for your equipment.
Processes | Takeout of molded parts |
---|---|
Helping you solve your problems |
|
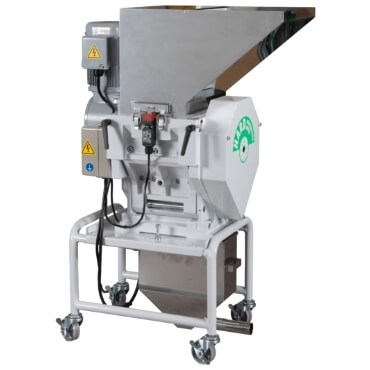
Our original cutting mechanisms are completely different from those of conventional grain cutters. In the sprues and runners, the material can be cut into grains close to the virgin material, which helps improve the recycling rate of your plastic materials. They can cut a wide range of materials, from soft materials to hard materials.
Processes | Cutting and mixing of raw materials |
---|---|
Helping you solve your problems |
|
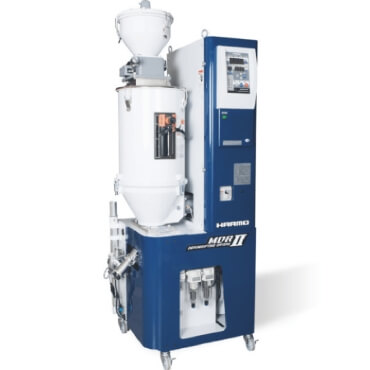
Our complete dehumidifying dryers help you achieve stable molding quality. Also, maintenance of these machines does not require any tools. They can easily be cleaned daily, when you change the materials, and this can help you streamline your set-up changes. We also provide a model with a helical hopper that removes dust, thereby reducing external defects.
Processes | Drying of raw materials |
---|---|
Helping you solve your problems |
|
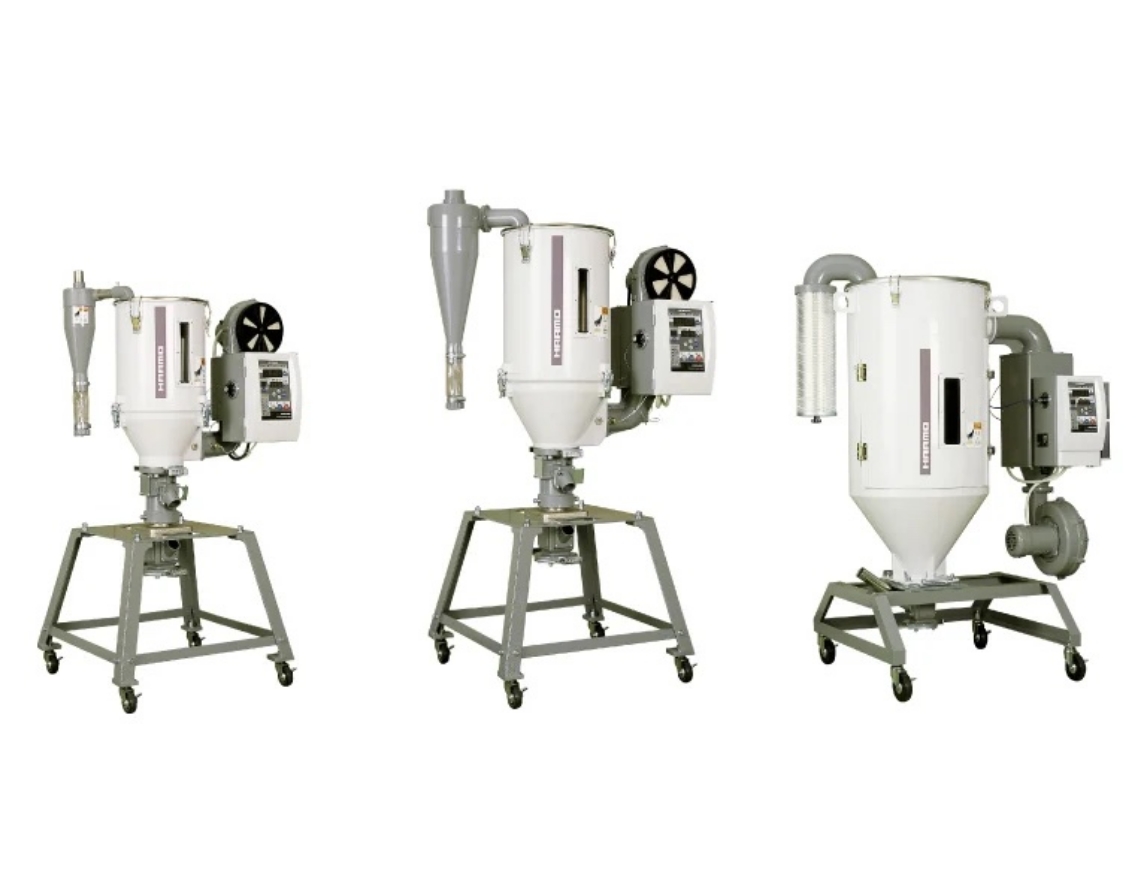
Hopper Dryer dries resin materials with hot air and is compatible with molding machines from 50 to 400 tons in size, with a lineup of temperatures from 120°C to 150°C maximum. Memory, timer, and warning functions help prevent errors and setup errors.
Processes | Drying of raw materials |
---|---|
Helping you solve your problems |
|
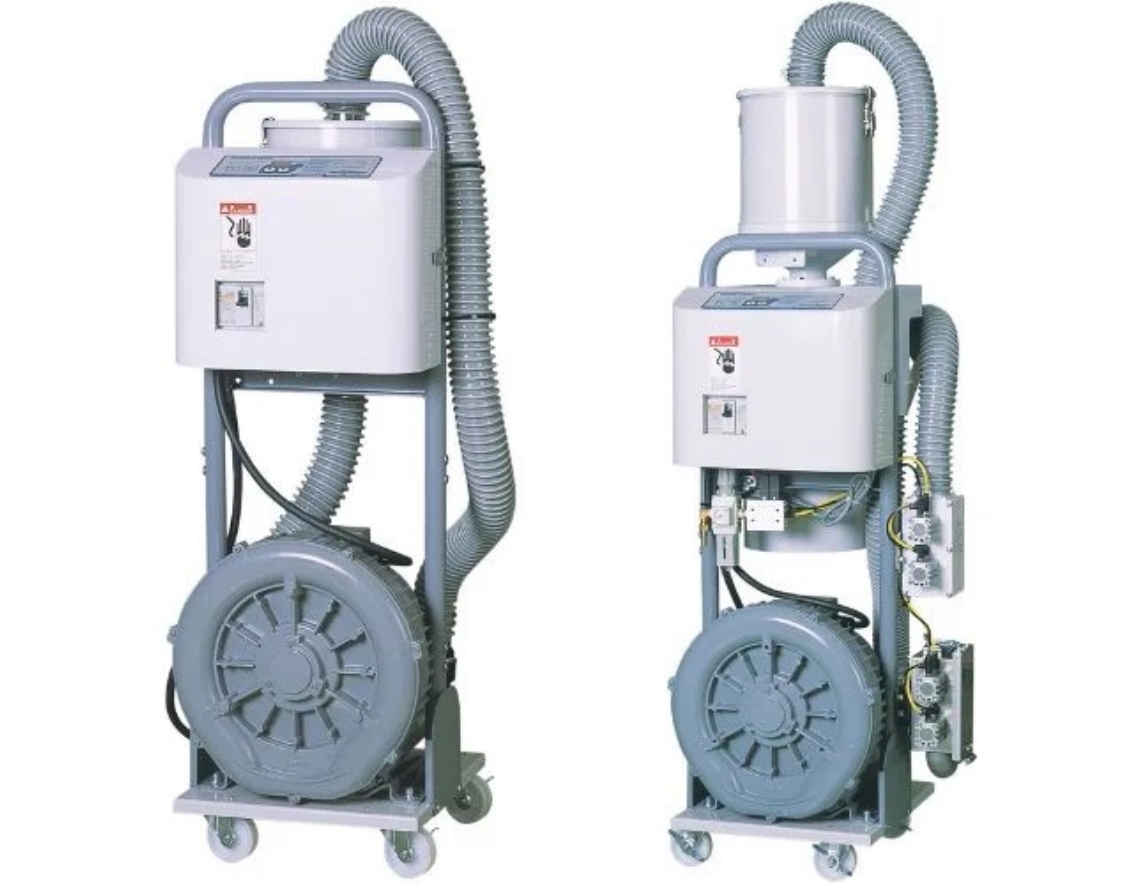
Hopper Loader used in resin material conveying lines, with a lineup of two types of conveying (single loader, twin loader) and two types of material handling (single material, mixed material). You can choose from 35 types to match the environment in which you will be using the machine.
Processes | Material Conveying |
---|---|
Helping you solve your problems |
|
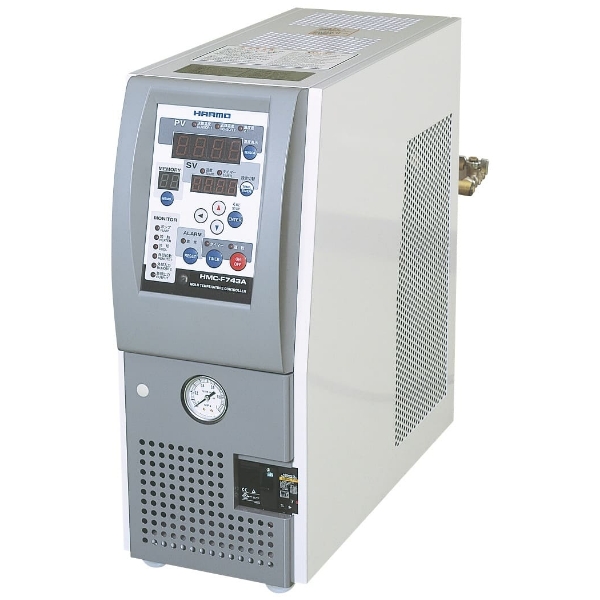
It is important to keep the temperature of the mold within a certain range in order to preserve the mold quality. If you purchase a temperature controller from our company, you can choose a model that uses oil as the cooling medium or a model that uses water. The mold memory function and start/stop timer function help you improve your work efficiency.
Processes | Mold temperature controller for molding machines |
---|---|
Helping you solve your problems |
|
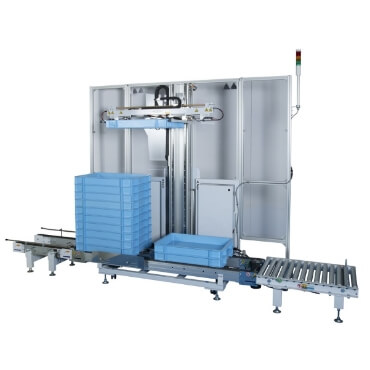
This system incorporates an input conveyor and an output conveyor to provide long-term stock automatically. Robots can palletize all products and stack molded products. We can flexibly provide solutions for any type of container that you use, so you will not need to buy new ones. This can help you reduce your initial investments.
Processes | Stock/palletize molded products |
---|---|
Helping you solve your problems |
|
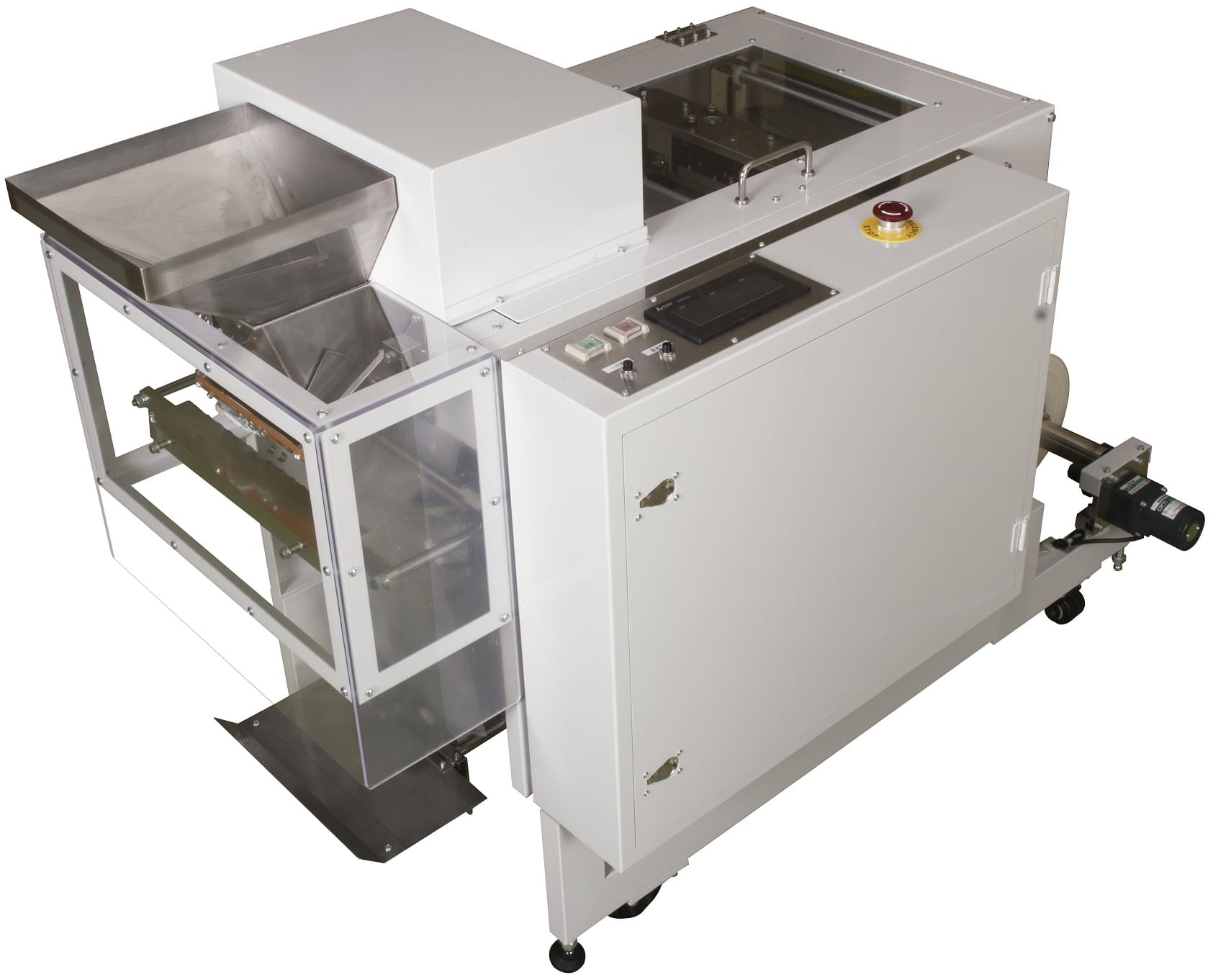
We provide a line-up of bag sizes from 100 mm to 300 mm. You can use tubular LDPE (low-density polyethylene) to make bags for packaging. If you choose the model that comes with a printer function, you can print QR codes, which can be used for product traceability.
Processes | Packaging of molded products |
---|---|
Helping you solve your problems |
|
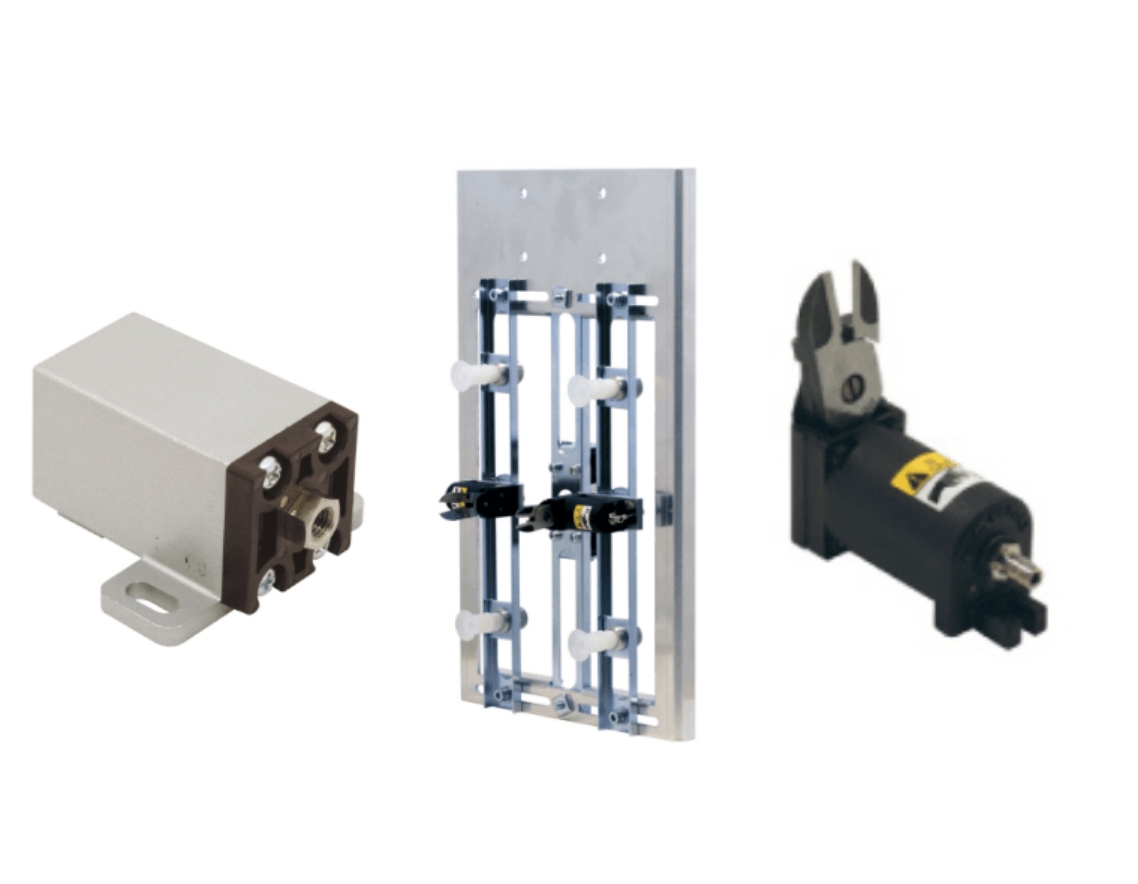
Attachment parts for chucks compatible with a wide variety of take-out robots. A wide range of combinations of components can be used for functions such as suction, gripping, and cutting, as well as for complex shapes of products. Customization is also available.
Processes | Takeout of molded parts |
---|---|
Helping you solve your problems |
|
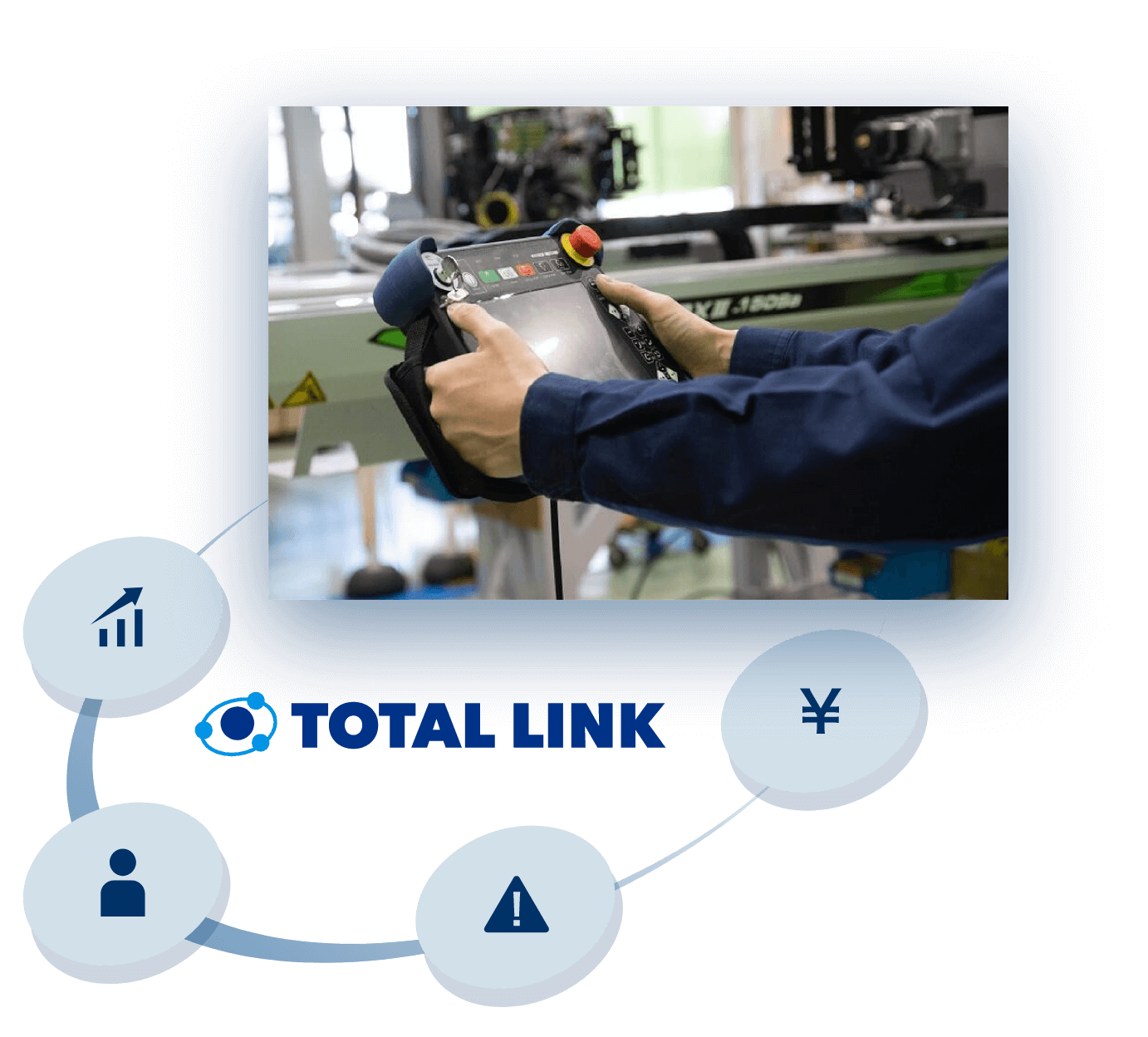
Total Link is a system that links injection molding peripheral devices to provide batch setting, start-up, and management, thereby allowing you to achieve automation, improved product quality, and cost reductions in your injection molding.
Total Link helps you resolve the issues that you have faced in the past. This is the kind of system that you would expect from HARMO, a company with more than 60 years of experience as a general manufacturer in the field.