- Top
- About HARMO
- Our vision
Our vision
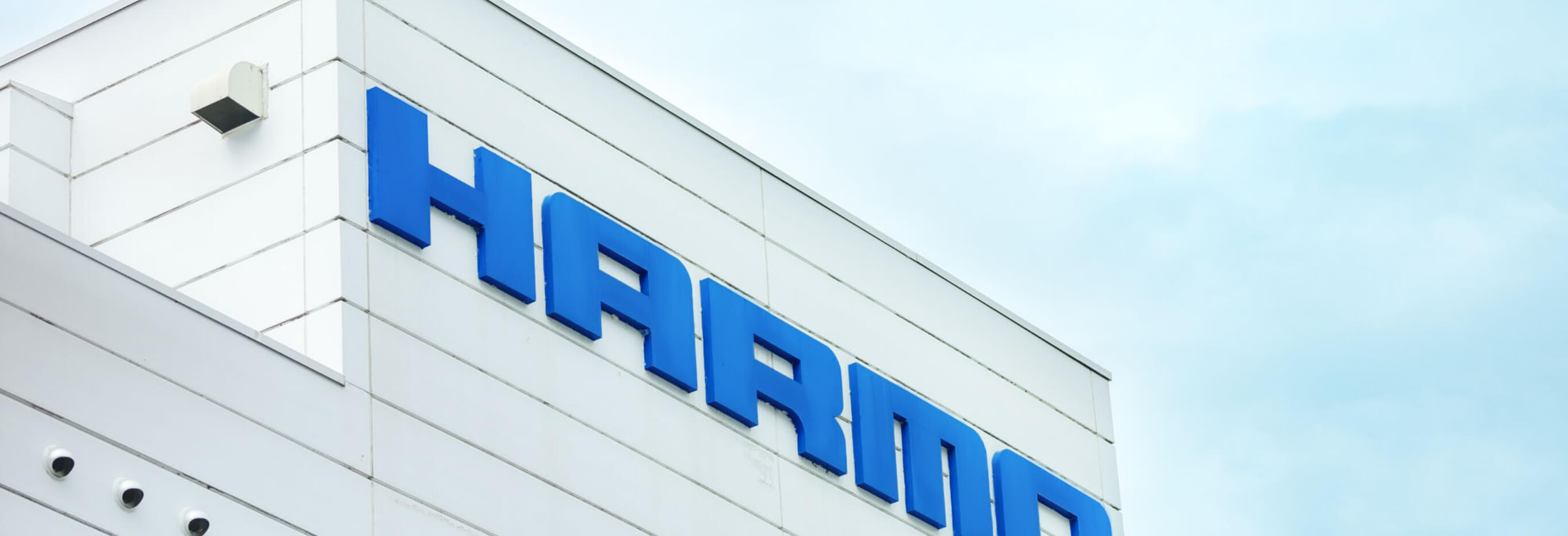
As Japan’s only comprehensive manufacturer,
Our goal is to become the No. 1 company in terms of customer satisfaction
- Deal with problems on the same day they arise
- Prioritize visualizing the future and never miss a deadline
- Be bold in your opinions and quick in your actions.
- Dedicate yourself to your work and learn from your mistakes
- Treasure your wisdom and nourish yourself with your labor
- Becoming “The No. 1 company in terms of customer satisfaction” in our sector
- Becoming the “only one company” that customers cannot do whithout
- Building a “Globally recognized HARMO brand”
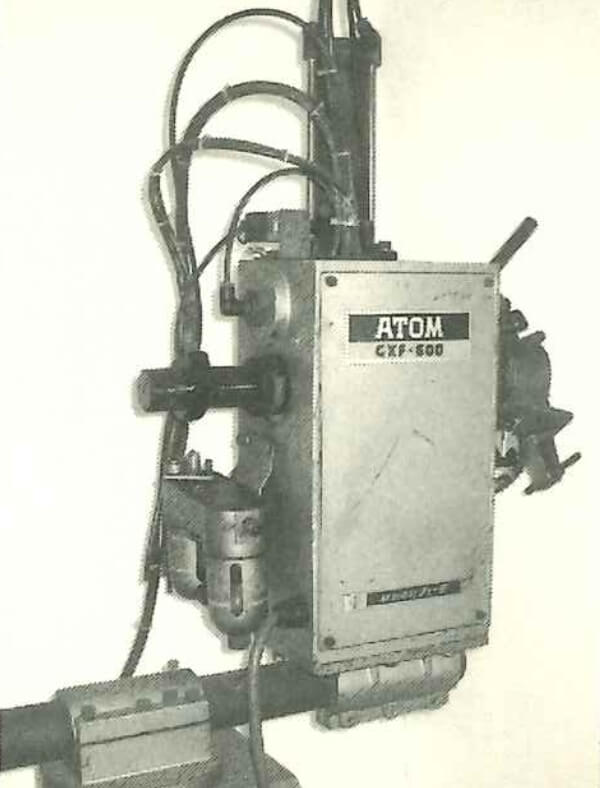
Shin-etsu Denshi Sangyo Co., Ltd. was established in Kohan, Okaya City, in Nagano Prefecture in 1962 and started developing, manufacturing and selling general automatic control devices. Two years later, the company was renamed HARMO Denki Co., Ltd.., and began producing automatic control devices primarily for the textile industry.
In 1969, the company produced the "ATOM" molded parts automatic take-out robot, the precursor of HARMO's current molded parts take-out robots. This development led to a change in perspective, based on the observation that focusing on the development of robots for injection molding machines might help the plastics industry in the future.
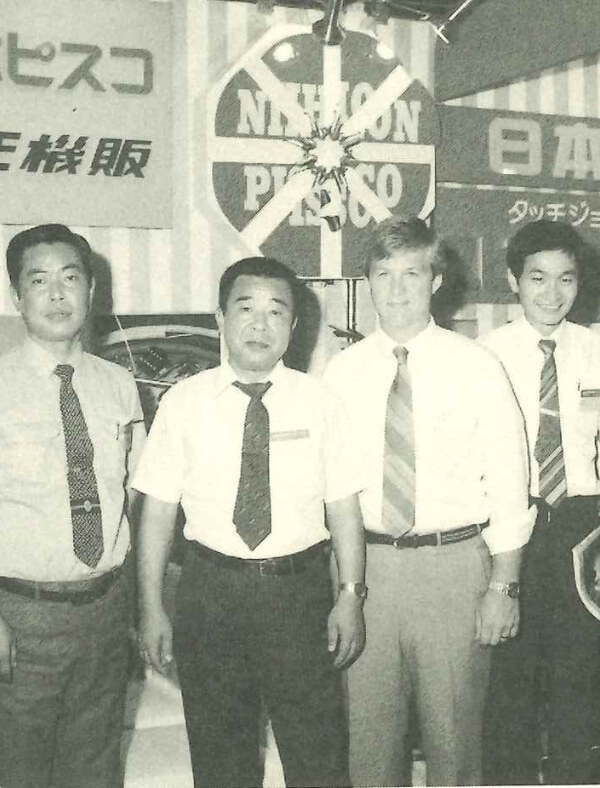
In 1972, the name was changed to HARMO Co., Ltd., and the company embarked on the dual path of increasing production of robots for injection molding machines and expanding its sales network.
The network was gradually expanded based on the idea that "you can't truly create things unless you actually go there and see what it’s like."
Becoming a familiar presence and offering after-sales service in addition to manufacturing and sales, helped customers develop a sense of security.
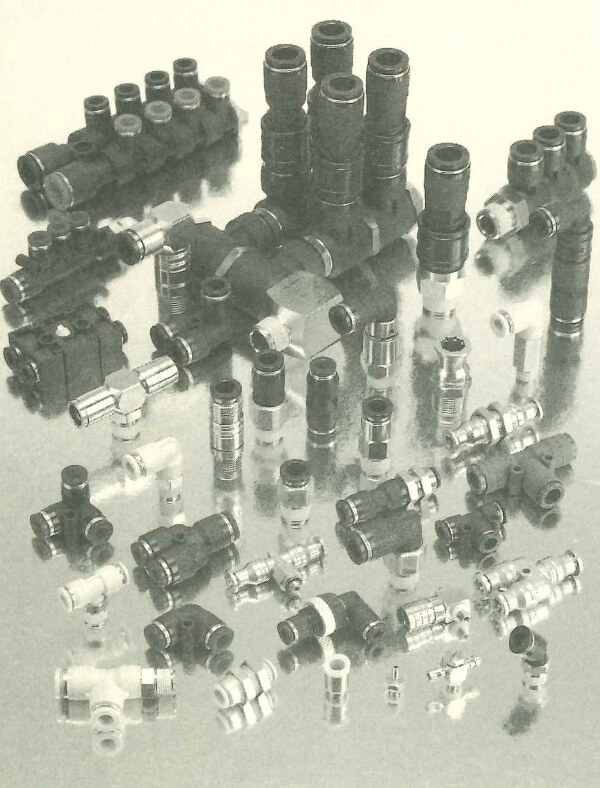
As a consequence of the first oil crisis, brass disappeared from the industrial stage and the company began researching and developing pneumatically controlled plastic knee- joints as a substitute for brass which led to the establishment of affiliated Group company NIHON PISCO Co., Ltd.
Take-out robots and plastic pneumatic joints became the two pillars of the company’s development; the shipping of products all over Japan led to an improvement in the company's reputation and brand power, and along with expanding its domestic network the company also began expanding overseas.
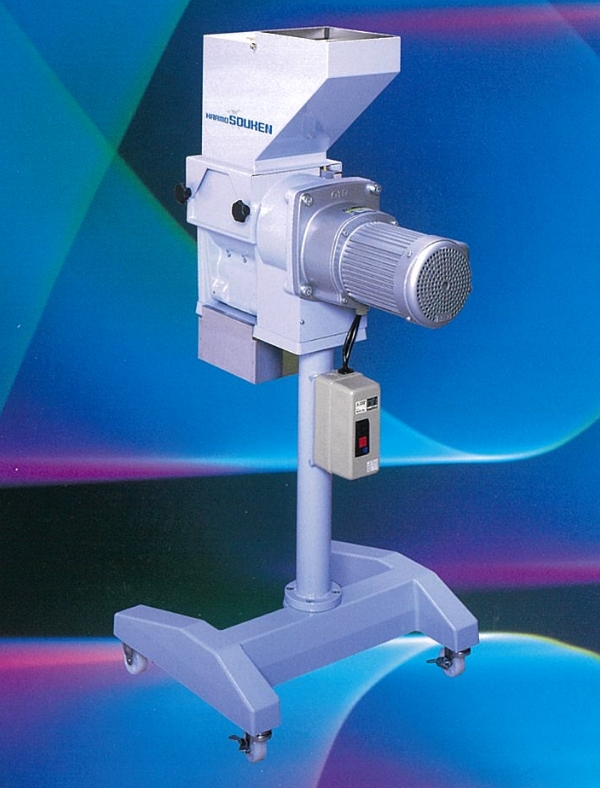
In the early 1990s, the economic bubble burst and HARMO's sales dropped by about half. In the middle of this predicament, HARMO T.E.C. (R&D) Co., Ltd. was established as a new company that would focus on product development.
The result of such research and development activities was the development of the gran cutter. The gran cutter, which makes it possible to reuse plastic scraps that were difficult to use with conventional crushers, anticipated the era of environmental awareness that was to come and became a guiding light out of those troubled times.
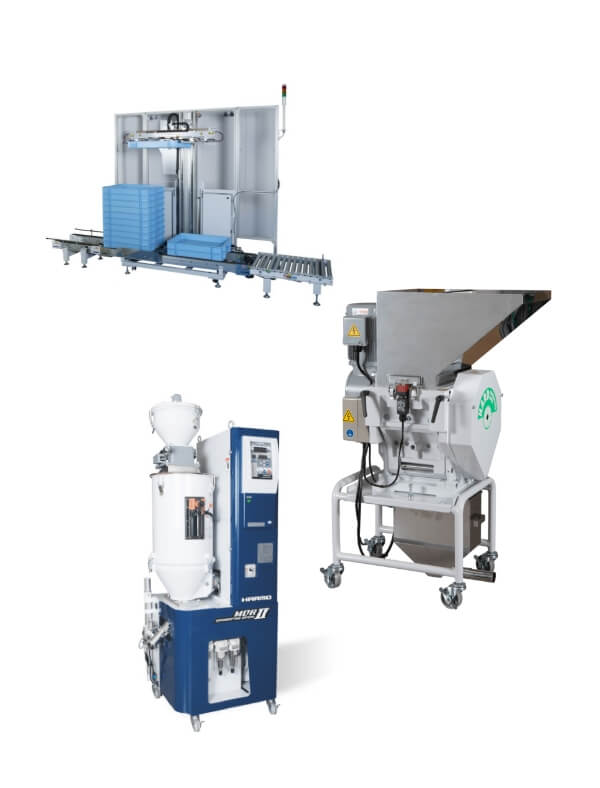
The gran cutter developed by HARMO T.E.C. (R&D) Co., Ltd. was first commercialized in the year 2000.
In response to feedback from production sites peripheral equipment like automatic stocking devices and dehumidifying dryers also began to be developed.
Furthermore, the “HARMO school” special education program was launched in 2009, targeting businesses that handled industrial robots.
It was during these years that the company established its position as a "comprehensive manufacturer of injection molding peripheral devices" by enhancing development, sales and after-sales support in order to meet market needs.
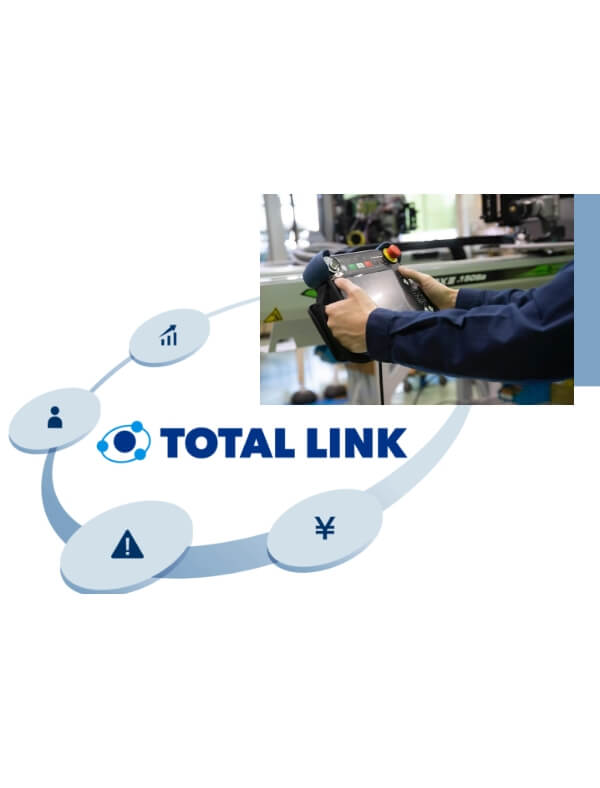
In 2017 the Total Link management system was introduced to further capitalize on the added value of being a comprehensive manufacturer. The system connects injection molding peripheral devices and collectively configures, activates and manages them, thus contributing to automation, quality improvement and cost reduction. It was the brainchild of HARMO, incorporating its more than 60 year-old track record and experience in research and development, in response to requests from production sites.
Faithful to the saying "we sell experience, not things," we continue to work tirelessly to assist our customers in solving their problems.
Partnering with friends who share our goals
I joined the company in 1990, immediately after the economic bubble burst. The hard times continued for a while, with major restructuring taking place and our main bank collapsing.
In 1998 I took over the company from my father and became president. In order to finally get out of the red and rebuild the company, all remaining employees joined forces and focused on developing new products.
That experience taught me that if we share a common goal and cooperate with each other we can get through anything. This applies not only to the company, but also to relationships with external parties like business partners. The fundamental thing is that all the people involved form a team and move forward together.
Earning the trust and satisfaction of our customers
In 1996, HARMO became the first in the industry to obtain the ISO9001 certification.
ISO9001 is an international standard for quality control systems, and its purpose is to ensure that customers can use our products and services safely and securely, and that they are satisfied. This idea is the foundation of HARMO's basic policy of "earning the trust and satisfaction of our customers."
In our work, we must give a shape to customers’ wishes and satisfy them.
To do that, we need to visit worksites, see conditions on the ground with our own eyes and listen to what the customer has to say. Such attitude is not limited to sales but applies to personnel in charge of development too. You can put your soul into your work only when you have confidence in what you do.
.jpg)
Proudly becoming an indispensable presence for the world
HARMO, as Japan’s only general manufacturer in the field of injection molding, is expanding its business activities overseas too.
We feel that there is a growing demand for "Made in Japan," which is why HARMO sticks to manufacturing in Nagano and is going to compete from there.
The growth of each employee leads to the growth of the company. Which is why we must think and act on our own, find out what we need to do and take pride in our work.
There is joy in working this way, and we believe that it leads to earning the trust and satisfaction of our customers.
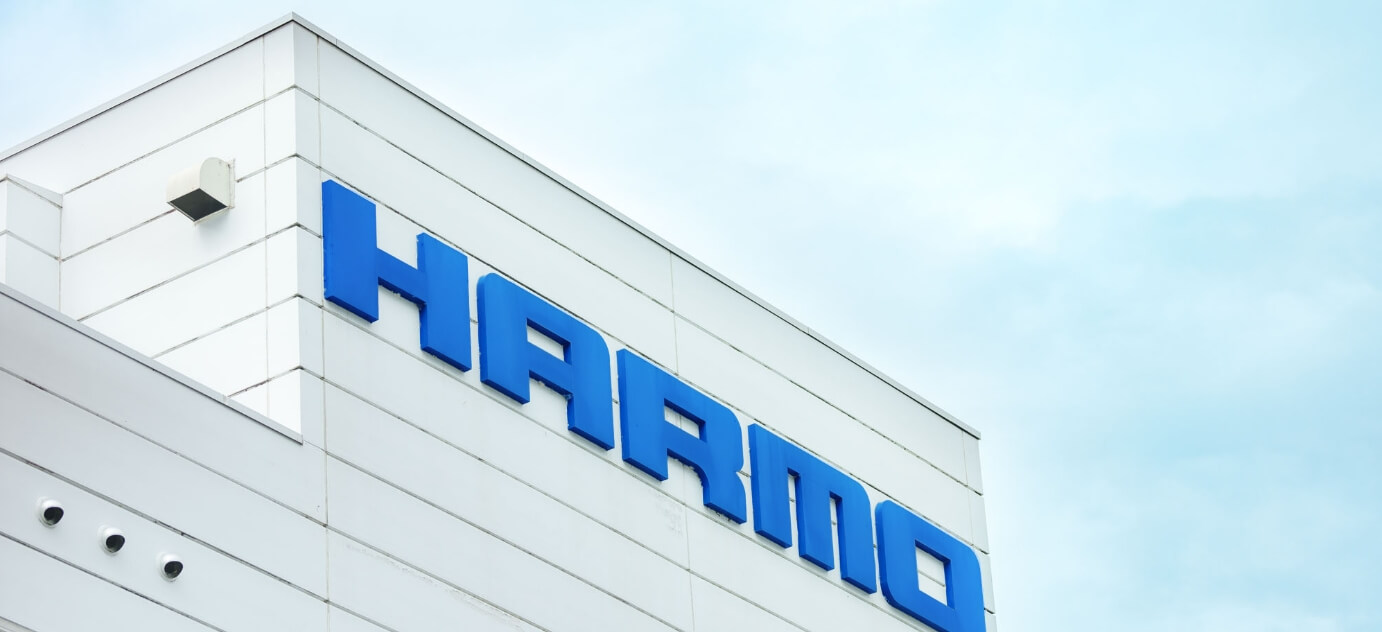